Labor cost percentage measures the portion of your sales spent on employee wages, benefits, and taxes. To calculate it, divide your total labor costs by your total revenue and multiply by 100, like $50,000 divided by $200,000 equals 25%. Industry benchmarks vary; retail typically ranges from 10-15%, while healthcare can be 30-40%. Understanding these figures helps you manage expenses effectively—keep exploring for detailed insights and strategies.
Key Takeaways
- Labor Cost Percentage measures the proportion of sales spent on employee wages, benefits, and payroll taxes.
- It is calculated by dividing total labor costs by total revenue, then multiplying by 100.
- Industry benchmarks vary: retail/hospitality (10-15%), manufacturing/construction (20-30%), healthcare (30-40%).
- Factors influencing benchmarks include industry type, business size, location, workforce skills, and seasonal demand.
- Accurate data and proper analysis are essential for meaningful insights and effective cost management.
Defining Labor Cost Percentage
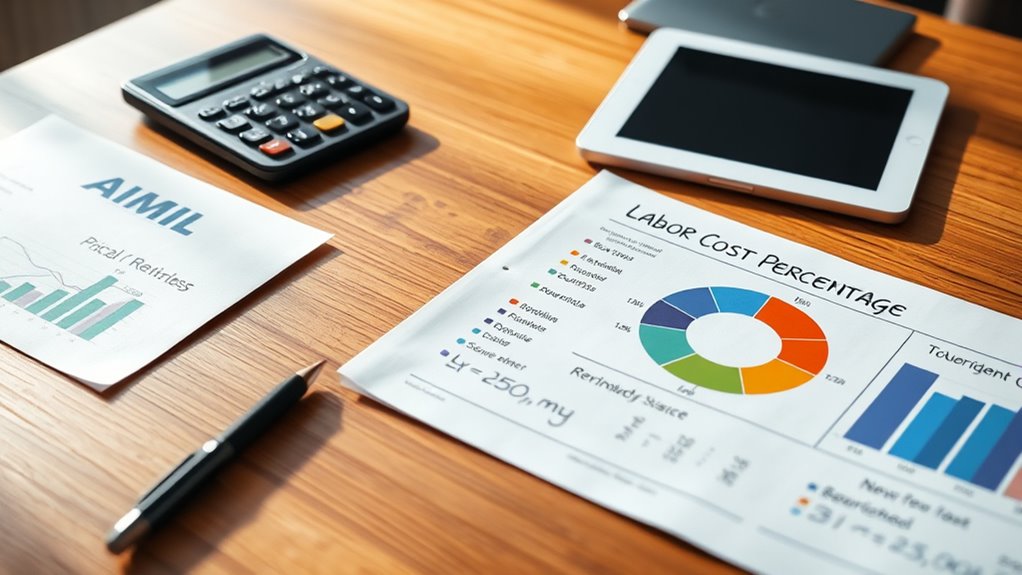
Understanding labor cost percentage is essential for evaluating how much of your revenue goes toward employee wages and related expenses. This metric measures the proportion of your sales that you spend on labor, including wages, benefits, and payroll taxes. To calculate it, divide your total labor costs by your total revenue, then multiply by 100. For example, if you spend $50,000 on labor and generate $200,000 in sales, your labor cost percentage is 25%. This figure helps you see how efficiently you’re managing labor expenses relative to sales. Keeping this percentage in check can indicate whether you’re over- or under-spending on staffing, which impacts profitability. Understanding this metric provides a clear picture of how labor costs fit into your overall financial health. Monitoring labor cost percentage regularly can help identify trends and areas for cost optimization.
Why Monitoring Labor Costs Matters
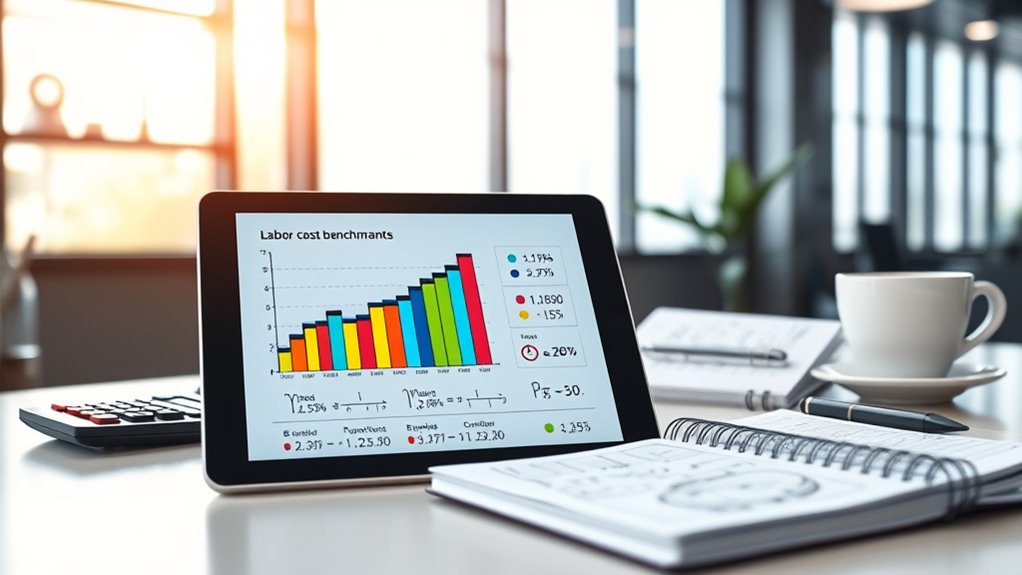
Monitoring your labor costs regularly helps you stay on top of your business’s financial health. When you track these costs consistently, you can identify trends, spot inefficiencies, and prevent overspending. This awareness allows you to make informed decisions about staffing, scheduling, and wages, ensuring your business remains profitable. If labor costs rise unexpectedly, you can investigate the cause and address issues before they become bigger problems. Additionally, monitoring helps you compare your expenses against industry benchmarks, highlighting areas for improvement. Without regular oversight, you risk falling behind on your financial goals or mismanaging resources. Staying proactive with labor cost management empowers you to maintain a healthy bottom line and supports long-term growth. Recognizing the impact of self-centered behaviors can also help you better understand internal dynamics that influence operational efficiency.
How to Calculate Labor Cost Percentage
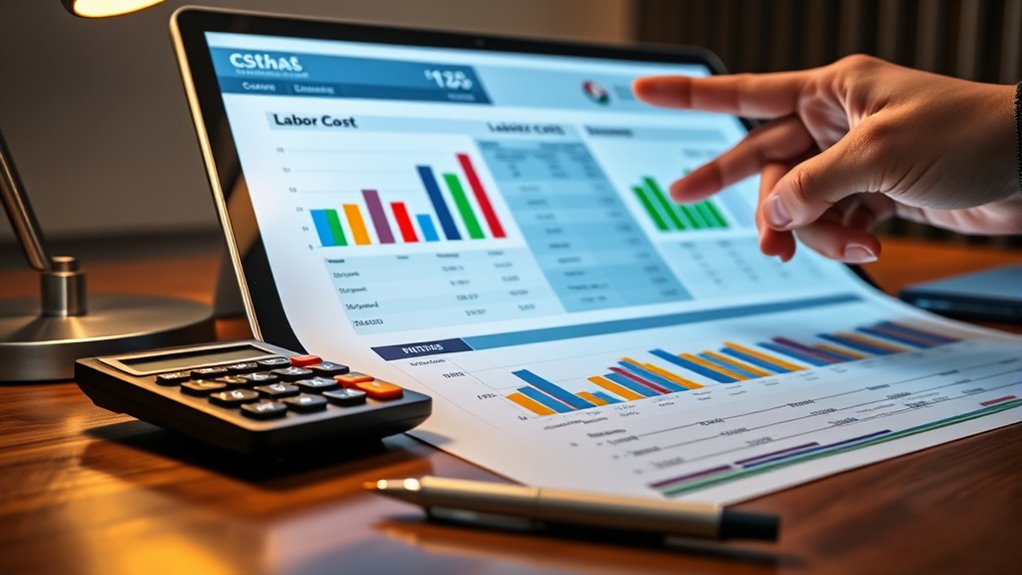
Ever wondered how much of your revenue goes toward labor costs? To find out, you need to calculate your labor cost percentage. First, determine your total labor costs, including wages, benefits, and payroll taxes. Next, find your total revenue for the same period. Divide your labor costs by your revenue, then multiply the result by 100 to get a percentage. For example, if you spend $50,000 on labor and have $200,000 in revenue, your labor cost percentage is 25%. This metric helps you understand how efficiently you’re managing labor expenses relative to sales. Regularly calculating this percentage allows you to identify trends, control costs, and make informed decisions to improve profitability. Keeping your calculations accurate is essential for cost management and gaining insights into your business operations.
Industry Benchmarks for Labor Cost Percentage
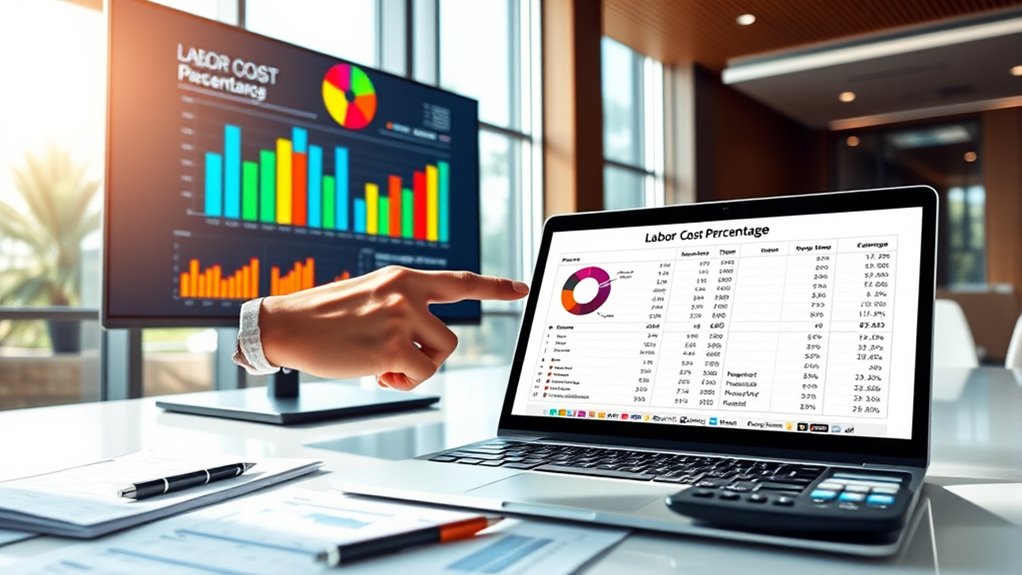
Industry benchmarks for labor cost percentage vary considerably across sectors, reflecting different operational models and profit margins. For example, retail stores often aim for 10-15%, while manufacturing might range from 20-30%. Here are some typical benchmarks:
- Retail & Hospitality: 10-15%, focusing on tight margins and high employee turnover.
- Manufacturing & Construction: 20-30%, balancing skilled labor costs with productivity.
- Healthcare & Professional Services: 30-40%, due to specialized skills and higher wages.
Understanding these benchmarks helps you gauge your company’s efficiency and identify areas for improvement. Keep in mind, these figures serve as guidelines; your ideal labor cost percentage depends on your industry, size, and business model. Comparing your numbers to these benchmarks can reveal whether you’re over or under-spending on labor. Additionally, monitoring labor cost management regularly ensures your business remains competitive and profitable.
Factors Influencing Labor Cost Variations
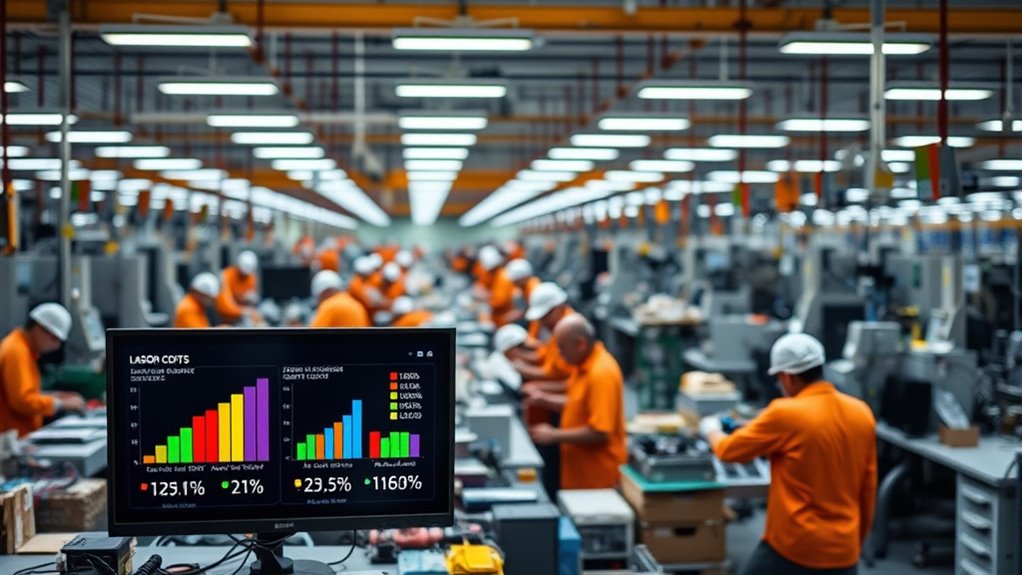
Several factors can cause labor cost percentages to vary substantially across businesses, and understanding these influences helps you manage expenses more effectively. First, the industry you operate in impacts labor costs—service sectors often have higher percentages than manufacturing due to labor intensity. The size of your business matters too; larger companies may benefit from economies of scale, reducing labor costs proportionally. Your geographic location influences wages and benefits, affecting overall costs. Additionally, your company’s productivity levels play a role—more efficient processes can lower labor costs as a percentage. Workforce skill levels influence wages and efficiency, impacting costs directly. Finally, seasonal demand fluctuations can cause labor costs to rise or fall temporarily, depending on staffing needs. Recognizing these factors enables you to better control and forecast labor expenses. For example, support hours can influence staffing costs and scheduling strategies.
Strategies to Improve Labor Cost Efficiency

To enhance your labor cost efficiency, start by analyzing current workflows and identifying areas where productivity can be boosted. Once you understand inefficiencies, implement targeted strategies. A good example is adopting electric bikes for delivery or commuting, which can reduce fuel and maintenance costs over time.
- Streamline Processes: Simplify tasks and eliminate unnecessary steps to reduce wasted time and effort.
- Invest in Training: Improve employee skills to increase speed and quality, reducing errors and rework.
- Optimize Scheduling: Align staff schedules with demand patterns to avoid overstaffing or understaffing, ensuring labor costs match workload.
Regularly monitor performance metrics to spot bottlenecks and adjust strategies accordingly. Adopting technology solutions, like automation tools, can also help increase efficiency. By focusing on continuous improvement and aligning labor with actual needs, you can control costs while maintaining productivity.
Common Mistakes in Calculating and Interpreting
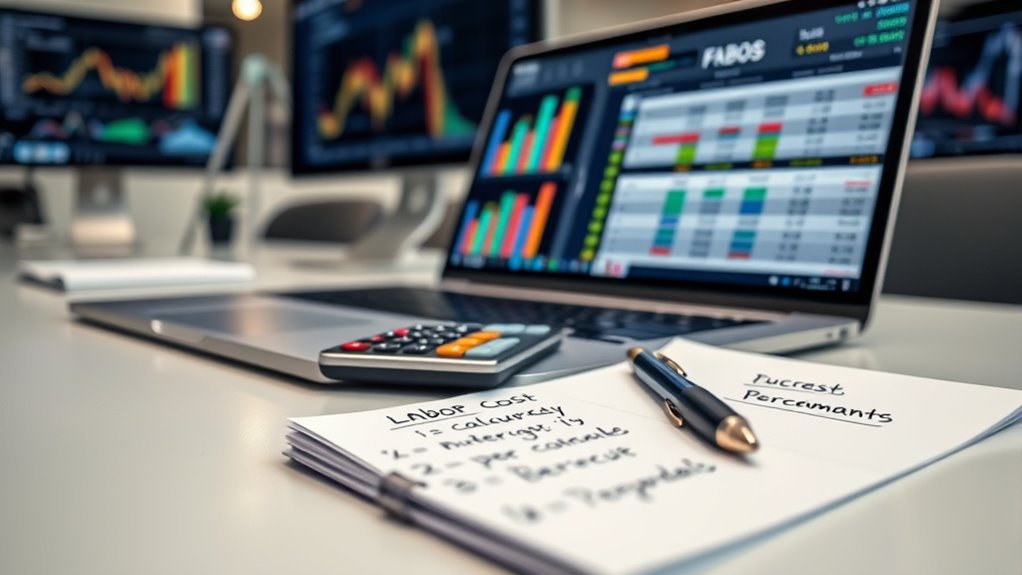
Many people overlook overhead costs when calculating labor cost percentage, leading to inaccurate results. Using outdated or incorrect data can also skew your understanding of labor efficiency. Additionally, misinterpreting ratios may cause you to make poor decisions about staffing and budgeting. Incorporating energy efficiency ratings into your analysis can provide a more comprehensive view of operational performance.
Ignoring Overhead Costs
Ignoring overhead costs is a common mistake that can substantially distort your understanding of labor cost percentages. When you omit overheads, you may underestimate the true cost of labor, leading to unrealistic profitability expectations. This oversight can cause you to make poor pricing decisions or misjudge project profitability. To avoid this, keep in mind: 1. Overhead includes rent, utilities, and administrative expenses that support your labor force. 2. Excluding overheads skews your labor cost percentage downward, giving a false sense of efficiency. 3. Accurate calculation requires adding overhead costs to direct labor costs before determining the percentage. Additionally, understanding the role of cost allocation is essential for precise labor cost analysis.
Using Inaccurate Data
Using inaccurate data can lead you to miscalculate labor cost percentages and draw wrong conclusions about your profitability. If you rely on outdated, incomplete, or incorrect figures, your ratio won’t reflect your true costs. For example, including only direct wages while ignoring benefits, taxes, and overtime skews the calculation. Similarly, using projected or estimated expenses instead of actual costs creates false impressions. Always verify your data is accurate, current, and thorough. Double-check your calculations and sources to avoid errors. Missing or misclassified expenses can considerably distort your labor cost percentage, leading you to make poor business decisions. Accurate data is essential for meaningful analysis, helping you identify real issues and opportunities for improvement. Never underestimate the importance of reliable, precise information in financial assessments. Incorporating comprehensive data ensures a more accurate reflection of your cost structure, enabling better strategic planning.
Misinterpreting Ratios
Have you ever misread a labor cost ratio and drawn incorrect conclusions about your business’s financial health? Misinterpreting ratios is a common mistake that can lead to wrong decisions. First, you might compare ratios across different industries without considering their unique benchmarks. Second, ignoring seasonal or temporary fluctuations can give a skewed view of your labor costs. Finally, focusing only on the ratio without understanding the context—like sales volume or profit margins—can mislead you into over- or underestimating efficiency. To avoid these errors, always compare ratios within relevant industry standards, analyze trends over time, and consider other financial metrics. Additionally, understanding financial ratios and their significance helps you interpret data more accurately. Accurate interpretation helps you make informed decisions, rather than reacting to misleading numbers.
Tools and Resources for Labor Cost Management
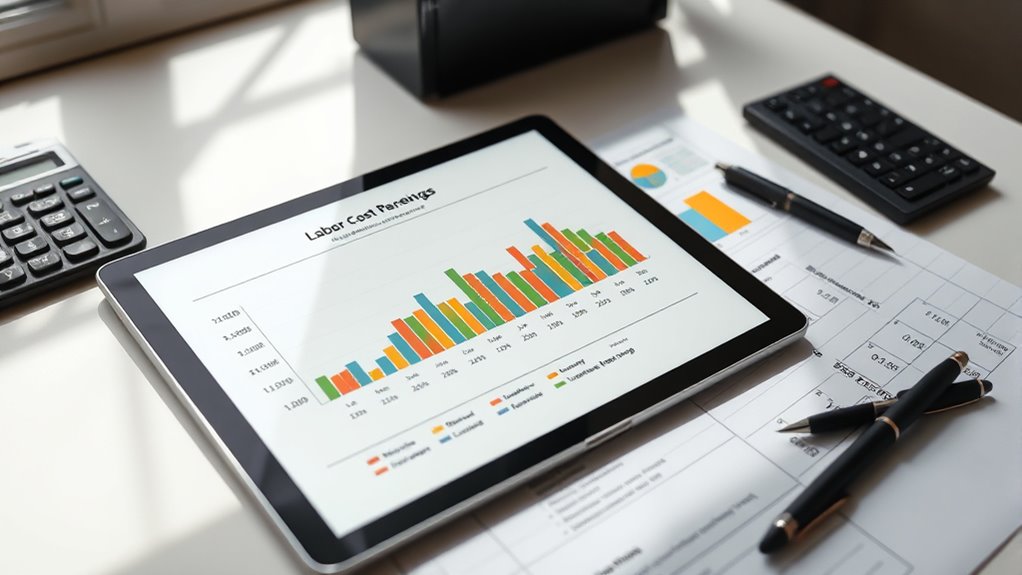
Effective labor cost management relies on the right tools and resources to provide accurate insights and streamline processes. Payroll software automates calculations, tracks hours, and guarantees compliance, saving you time and reducing errors. Budgeting and forecasting tools help you set realistic labor cost targets and adjust plans as needed. Time-tracking apps give detailed data on employee hours, enabling better resource allocation and payroll accuracy. HR management systems streamline onboarding, scheduling, and performance tracking, aligning labor costs with productivity. Additionally, analytics platforms analyze trends, identify cost-saving opportunities, and monitor key metrics like labor cost percentage. Combining these tools empowers you to make informed decisions, optimize staffing, and control labor expenses, ultimately improving your business’s financial health.
Frequently Asked Questions
How Often Should I Review My Labor Cost Percentage?
You should review your labor cost percentage regularly to keep your business profitable. Ideally, do this monthly or quarterly, depending on your industry and fluctuations in sales or staffing. Regular reviews help you spot issues early, adjust staffing levels, or control costs proactively. Keep an eye on trends, and don’t wait too long—being proactive guarantees your labor costs stay aligned with your revenue goals.
Can Labor Cost Percentage Vary Significantly Within the Same Industry?
Did you know that labor cost percentages can vary by up to 20% within the same industry? You might find that your business’s labor costs differ markedly from competitors due to factors like operational efficiency, location, or workforce skills. This variation means you should regularly analyze your own numbers and compare them to industry standards, ensuring you’re managing costs effectively and staying competitive in a dynamic market.
What Are the Best Software Tools for Tracking Labor Costs?
You should consider software tools like QuickBooks, ADP Workforce Now, and SAP SuccessFactors for tracking labor costs. These platforms offer real-time data, detailed reporting, and user-friendly interfaces, helping you monitor expenses accurately. By integrating payroll, time tracking, and project management, you gain better control over labor costs, identify inefficiencies, and make informed decisions to improve profitability and operational efficiency within your industry.
How Does Seasonal Demand Affect Labor Cost Benchmarks?
Imagine your labor costs as a rollercoaster, soaring during peak seasons and plummeting in the off-season. Seasonal demand makes benchmarks fluctuate wildly, so you need to stay alert. You might find yourself adjusting staffing levels or budgets more often, like a tightrope walker balancing on a moving line. Keep a close eye on these shifts, so your labor costs stay manageable regardless of the seasonal twists and turns.
What Impact Does Employee Productivity Have on Labor Cost Percentage?
You see, employee productivity directly impacts your labor cost percentage. When your team works efficiently, you get more output for each dollar spent on labor, lowering your percentage. Conversely, if productivity drops, you’ll need to spend more to achieve the same results, increasing your labor costs relative to sales. Improving worker efficiency helps control costs and keeps your labor expenses aligned with your business goals.
Conclusion
Think of your labor cost percentage as a compass guiding your business through stormy seas. When you keep it steady, you navigate smoothly toward growth. But if it drifts too high or too low, you risk hitting hidden rocks. By understanding and managing this essential metric, you steer your ship with confidence, ensuring every crew member’s effort propels you forward. Stay vigilant, and let your labor costs be the steady wind behind your success.